Interface Fluidics is a leader in creating microfluidic reservoir-mimicking chips, which we use to conduct a variety of measurements. When designing microfluidic systems, many factors must be taken into account. One of these is capillary pressure.
So, what is capillary pressure? It’s defined as the pressure that is generated when two immiscible fluids are in a narrow channel or tube. This pressure becomes important when describing fluid flow in an oil reservoir because the interaction between the interfacial tension, contact angle, and rock pore diameter has a large impact on the flow regime in the rock.
The reading also gives invaluable information to determine the oil zone, transition zone, and water zone underground to help determine where well perforation should be conducted to produce oil.
The capillary pressure equation
In a horizontal system, the Young-Laplace equation describes the pressure acting on a fluid that is forcing it to flow into a capillary tube or microfluidic channel. The interfacial tension is a key parameter which largely affects the resulting pressure.

In this equation, the interfacial tension is a key parameter which largely affects the resulting pressure.
Surfactants, lower interfacial tension by adsorbing to the boundary (of water and oil, for example) and are widely used in the oil and gas industry. Interface has worked with different companies on surfactant screening and optimization, including hydraulic fracturing, foam surfactants for SAGD, and enhanced oil recovery projects.
The pressure that is drawing fluid downward is due to the force of gravity and the density difference between the wetting and non-wetting phase.
A microfluidic system can be designed to take advantage of capillary pressure to either encourage or discourage flow. Many common microfluidic tests, like COVID-19 antigen tests, use a lateral flow assay that takes advantage of capillary pressure to drive flow along the test strip.
In horizontal systems, the impact of gravity on the fluids in a microchannel is negligible. Interface’s microfluidic devices (except for SAGD) have microchannels that are flat and only a few microns tall. This diminishes the effect of gravity on our tests.
In contrast to a bond number, the capillary pressure in a horizontal system is not competing against gravity and can be utilized to transport fluids efficiently.
In this video, a dye droplet is driven through a horizontal capillary tube due to the effect of capillary pressure.
In a vertical capillary system with a wetting liquid and a non-wetting gas phase, there are two forces acting on the fluid in the tube:
- The force of gravity drawing the fluid down
- The interfacial tension of the fluid acting along the circumference of the capillary which is drawing the fluid up the tube
If the liquid is the non-wetting phase, both forces act down, and the boundary will be below the surface of the bulk liquid.
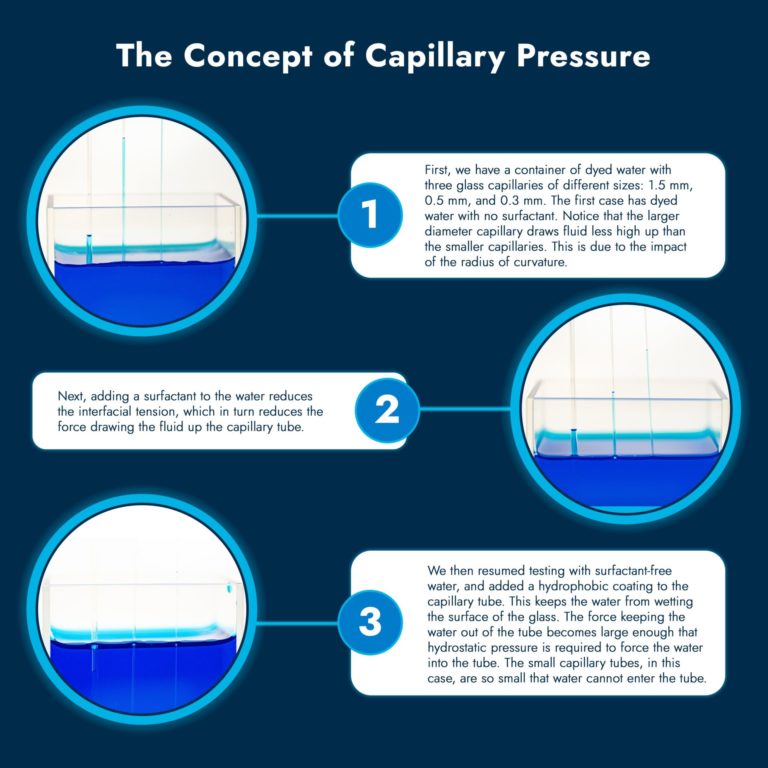
How does this tie into reservoir production?
Depending on the reservoir rock wettability, capillary pressure can act either as a driving force or a repulsive force.
In the case of water-wet reservoirs, water flooding can be more effective as the capillary force helps water more easily penetrate the reservoir pore spaces, particularly smaller pores, resulting in a better displacement efficiency and higher oil recovery.
Conversely, the effectiveness of waterflooding reduces in the oil-wet reservoirs where it is harder for the water phase to conquer capillary pressure in the smaller pores to displace the oil phase.
It’s been estimated that capillary pressure for a primary-drainage invasion-percolation process in a sandstone rock with a typical pore radius of 10 microns is in the order of a few kPa. The following figure shows capillary pressure as a function of water saturation.
For a primary drainage system shown in the above figure, oil will not displace water until a minimum critical capillary pressure is reached known as Pcentry.
Oil will then fill out wider throats first then as it reaches narrower ones, capillary pressure increases until in it reaches a value where no more water can be removed as drops are trapped in the corners. This is referred to as the irreducible water saturation.
At Interface Fluidics, we are conscious of capillary pressure when designing our systems as it impacts the type of flow we see on our microfluidic chips. It is especially pronounced when we work at the nanoscale, such as in our flowback screening. However, our systems operate at such high temperatures that we often cannot rely on it.
For example, Interface works with microfluidic channels with hydraulic radii that can be less than 2.3 μm using various petroleum products. This can result in capillary pressures in the 45 KPa range. This figure is even greater when working with nanofluidics.
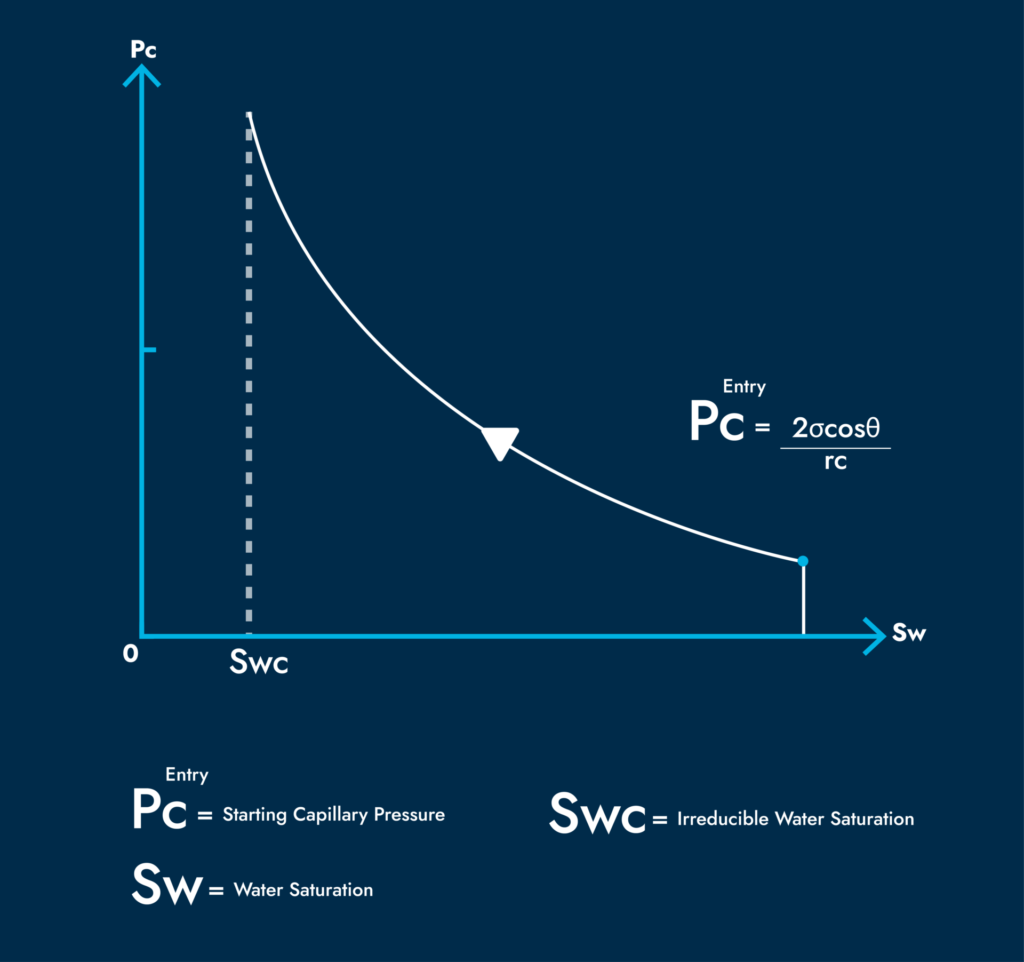
Although one of many key factors, capillary pressure is useful to petroleum engineers for a variety of reasons. It can be used to evaluate reservoir rock quality, pay vs. non-pay, expected fluid saturations, seal capacity, depth of reservoir fluid contacts, transition zone thickness, and approximating recovery efficiency during primary and secondary recovery.
Find out more about Interface’s screening capabilities on our Solutions page.