By definition, microfluidics is the science and technology of analyzing or processing fluids in channels from 1 to 1000 microns in diameter. Put in perspective, a single strand of hair is around 100 microns wide. The use of this technology in the oil and gas industry has a complex history that brings together aspects of molecular analysis, biodefense, molecular biology, microelectronics, and reservoir engineering.
While it has its roots in biomedical science, a biomedical-to-energy transition arrived following a boom in microfluidics for health applications over the last two decades. It came with advances in microfluidic chip fabrication techniques and microscopy, which greatly expanded relevant fluid analysis capabilities.
A recent review article by Interface Fluidics published in Energy & Fuels shows the evolution of this budding field within the energy industry. It highlights major past achievements, recent milestones and looks ahead to future opportunities presented by an energy transition.
What is microfluidics for the oil and gas industry?
Oil and gas microfluidic testing falls into two broad categories. Flow-through porous media involves creating a physical replica of the rock and observing fluid interactions at the pore scale at relevant conditions. Meanwhile, reservoir fluid analysis is about determining the reservoir fluid properties under reservoir conditions.
Pore-scale dynamics of in situ processes often encompass water flooding, polymer flooding, chemical and foam injection, gas flooding, and thermal solvent processes. In contrast, reservoir fluid property measurements include bubble and dew points, solution gas-oil ratio, solubility and diffusivity, minimum miscibility pressure (MMP), wax crystallization, and asphaltene precipitation.
Interface Fluidics scientists have made significant contributions to the aforementioned fields in a variety of publications. This includes a major addition that resolves porous transport and quantifies scale-dependent variations in phase properties with unprecedented accuracy.
Microfluidic technology offers many benefits over traditional beaker-scale chemical analysis or large-scale core flood or sand-pack flood testing. Advantages of microfluidics include:
- It requires a small sample size in the order of milliliters for a set of tests. This is important for downhole samples that are expensive to retrieve or for prototype chemistry that has not been synthesized yet in large quantities.
- Increases accuracy and precision of measurements due to the micro-scale imaging and precise control of fluid interactions.
- It produces rapid results as fluid interactions can be observed over hours instead of days or weeks.
- It provides a much safer testing environment because the contained energy within testing devices is tiny – stemming from the small sample size required.
Early days of research
Research in this field was largely enabled by F.S. Kipping’s study of silicon in 1927 and the invention of photolithography in the 1950s.
Fluid analysis itself has been informing oil and gas operations since the industry’s inception. A pioneer in the field, Dr. Oliver C. Mullins, provided the foundation for downhole fluid analysis (DFA). He also led the research on the Yen-Mullins Model of asphaltenes and reservoir fluid geodynamics (RFG). RFG marked an important milestone in the field and provided a comprehensive suite of fluid analysis tools.
However, fluid analysis has historically been resource-intensive, requiring long run times and a major investment in capital and labor. The advent of microfluidics has changed this.
Innovation in this field began with microfabricated physical models representing the pore-scale of underground reservoirs, also known as micromodels. These devices were first developed to investigate microscale fluid behavior and played a big role in studying fluid-fluid and fluid-solid interactions.
The first micromodel consisting of glass beads between two plates was developed in 1952. However, this system presented interfaces that were difficult to interpret.
A decade later, the first etched-glass micromodel was constructed to study the effect of wettability on waterflood oil recovery. 2D networks were developed later in the decade using a photoresist that enabled the reproduction of any network pattern made from a photograph or generated by a computer.
This early use of etching and photoresists contributed significantly to future research. Combining photolithography and etching steps led to the influential invention of microscale gas chromatography on a silicon wafer in the late 1970s.
By 1986, 2D and 3D micromodels with various patterns had been prototyped using Hele-Shaw and glass-bead models, optical lithography, etching method (wet, dry, laser, or plasma), stereolithography (or 3D printing), resin molding, and soft lithography.
On the fluid observation side, the arrival of imaging techniques like optical and confocal microscopy enabled the study of micromodels over a broad range of length scales. Another notable achievement involved advancing the fabrication and bonding of glass devices.
In the 1990s, a revolution took place as microelectronic fabrication techniques were adopted by biologists. These techniques allowed for extremely accurate patterns to be transferred onto glass, silicon, or newly developed soft polymers. Scientists used this technique to create miniature gas chromatographs, detect disease in body fluids, analyze cells, and even create organ on a chip systems.
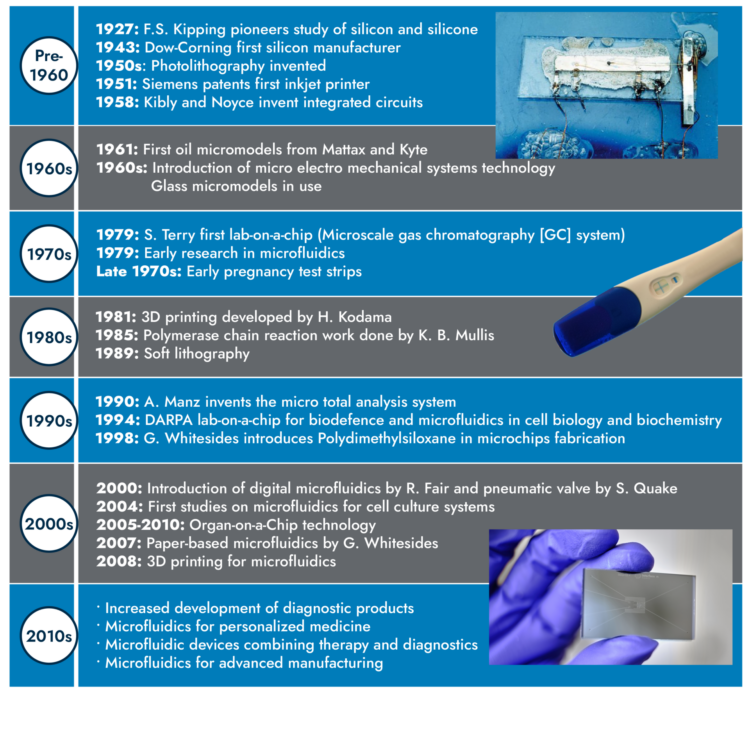
Applying technology to modern oil and gas operations
Early microfluidics applications were limited in terms of pressure and temperature. Only recently have reservoir relevant conditions of 1000 bar and 200 ℃ been achieved. Interface Fluidics was the first to do so commercially. Deviating from healthcare applications, oil and gas testing requires much higher pressures but avoids sterility requirements.
To transition microfluidics to high-pressure, high-temperature (HPHT) measurements, both the pressure capability of the chip and the external fluidics system had to be increased while maintaining high-resolution optical access.
This led to glass-glass and silicon-glass emerging as the best material choices for the chips.
While advances in material science and chemical synthesis significantly contributed to HPHT applications, developing an interconnect suitable for HPHT proved challenging.
Microfluidics research groups used compressing fittings and O-rings to achieve a pressure of 300 bar at temperatures of 450 ℃ and a pressure of 450 bar at room temperature around a decade ago.
Systems with similar interconnects were developed based on this work due to its simplicity and robustness. These studies measured:
- Gas-oil ratio (at 376 bar & 15 ℃)
- Full pressure-temperature phase diagram (at 67 bar and 90 ℃)
Interface Fluidics has advanced this work to determine:
- CO2 in oil solubility, diffusivity, extraction pressure, miscibility, contact angle (at 130 bar & 50 ℃)
- CO2 dew point measurement (at 144 bar & 50 ℃)
- MMP measurements (at up to 350 bar and 144 ℃)
Another approach housed the chip in a pressure tank where it and the interconnect experience relatively low-pressure differentials (with surrounding hydraulics providing overburden pressure).
These advances have led to a handful of companies offering microfluidics services in energy. Out of them, Interface Fluidics stands out by commercializing measurements for flowback, foam studies for enhanced oil recovery (EOR), and MMP.
Going nano
Most classical theories and tools developed for conventional hydrocarbon reservoirs typically had high permeabilities and large pore size distributions. These tools then fell short when employed for tight unconventional formations.
Unconventional oil and gas operations emerging in the late 90s involved production from formations with an extreme level of nanoconfinement. They required tools to analyze complex fluid transport and properties at the nano-scale, including anomalies that could either promote or impede fluid flow.
This led researchers to focus on nanofluidics for energy starting about a decade ago. Nanofluidics had also been previously developed for biomolecule analysis, which facilitated the transition. Soon after, nanofluidics surpassed classical methods and gave unconventional operators a better window into their reservoirs.
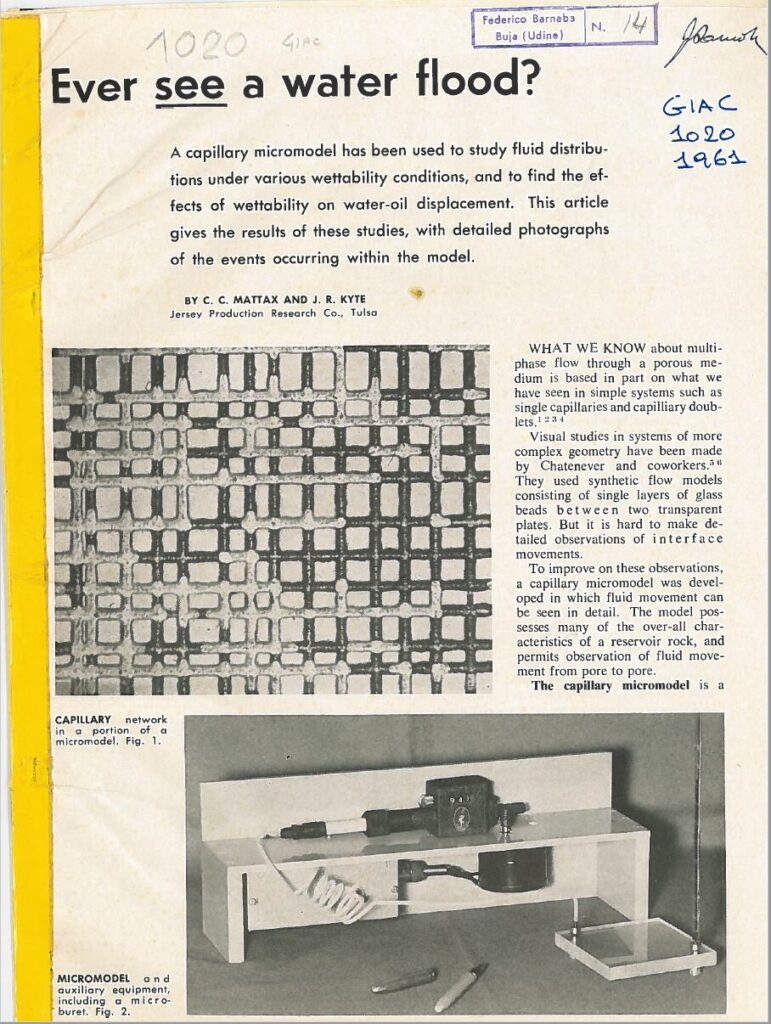
With contributions from Interface Fluidics-associated scientists, significant research milestones in nanofluidics include:
- A nano model that assessed the potential of CO2 injection for EOR of tight formations.
- Measurement and quantification of the first contact MMP of a decane-CO2 system at 50 nm confinement.
- Development of a dual-porosity dual-permeability nanoporous media to quantify the flowback performance and pore-scale damage mechanisms of a wide range of chemicals used in hydraulic fracturing.
- Analysis of the evaporation rate and flow regime of light hydrocarbons within sub 10 nm to determine fluid transport and production rate of tight gas formations soon followed.
- Exploration of hydrocarbon phase transition using nanofluidic devices at sub 10 to 100 nm.
Nanofluidics is clearly important for a wide range of measurements and applications. For example, nanofluidics in hydraulic fracturing gives a potential reduction in water and chemical usage while optimizing operations.
Commercial surfactants production emits 4.7 tonnes of CO2 per tonne of surfactant produced, so cutting down on them is important both for cost-saving and environmental benefits.
Secondly, using fresh water in unconventional operations poses risks to the environment and water security. However, there is a lack of information on the performance of recycled brines with differing total dissolved solids (TDS) levels. Nanofluidics can help bridge this knowledge gap, thus enabling a switch to produced/recycled brine.
Addressing these challenges with microfluidics and nanofluidics, as Interface is doing, can result in a large reduction in aggregate CO2 emissions, helping the energy industry strive toward net-zero carbon emission goals.
Geochemistry within reach
While micro and nanofluidic analogues replicate reservoir temperature, pressure, fluid composition, and geometries, they aren’t yet able to capture geochemistry.
Glass and silicon are usual chip materials that can withstand high pressures and temperatures while being highly inert. This provides a reaction-free environment where other variables can be studied, such as multiphase transport and fluid-fluid interactions.
However, fluid-rock interactions are critically important in applications such as EOR and geological storage. Glass and silicon can appropriately represent the mineralogy of sandstone formations but fall short in mimicking other geological formations such as carbonates, organic-rich shale, and coal-bed methane formations.
As of this writing, there are no commercialized products in this space. Research has included real rock micromodel approaches and the use of crushed grains and rocks to generate microporous structures for exploring immiscible displacement processes. It is expected that the commercialization of geochemistry-enabled devices will advance as CO2 sequestration proliferates in the years ahead.
Looking to the future
Microfluidic screening services provided by Interface offer savings, reduce chemical use, tune process operating conditions, and improve reservoir production. It is also the only organization that has been able to commercialize this technology in oil and gas.
Microfluidics is expected to play an important role in the energy transition required to reach net-zero emissions by 2050. Carbon management applications like CO2 EOR could play a role now, with geological storage and sequestration having potential in the long term.
For now, carbon dioxide injection faces challenges such as tuning the injection fluid and conditions to avoid reservoir damage as well as pore blocking and permeability reduction by salt precipitation in saline aquifers.
Microfluidics can contribute in several ways here, such as providing visual evidence of stored gas security and quantifying mineralization and reactions.
A recent, notable development by Interface is a microfluidic platform to measure the MMP for CO2-EOR, which can lower the threshold required to obtain on-demand relevant data at reservoir relevant extreme conditions.
CO2 utilization and sequestration are complex processes that require PVT and fluid phase behavior measurements. New innovations are needed to accurately report PVT properties of CO2 with different fluid systems and to incorporate geochemistry to gain insights into reactive transport such as salt formation.
Microfluidics will also play a vital role in direct air capture of the greenhouse gas by developing CO2 capture materials and fluids, which will require screening similar to current PVT testing.
Interface opens the door for commercial microfluidics
While working with David Sinton at the University of Toronto, Interface CTO and Co-Founder Tom de Haas worked to create an HPHT microfluidic platform. Their goal was to reduce the time and investment required to implement new technology in Alberta’s oil sands.
After showing success, this technology provided a major advance in understanding the mechanisms at play inside a SAGD reservoir, and in 2016 Interface Fluidics was born. Since then, the company has continued developing technology to increase the kinds of tests and conditions that can be operated by its platform.
Constant improvement is paramount at Interface Fluidics, as evidenced by our pressure capabilities. Starting with the premise that the energy industry needed HPHT microfluidics, Interface has been able to exponentially grow its capabilities over time.
It’s imperative to increase temperature and pressure capabilities to replicate a wider range of real-life reservoir conditions. Today, Interface can accurately match measurement temperature and pressure to more than 80% of the world’s reservoirs.
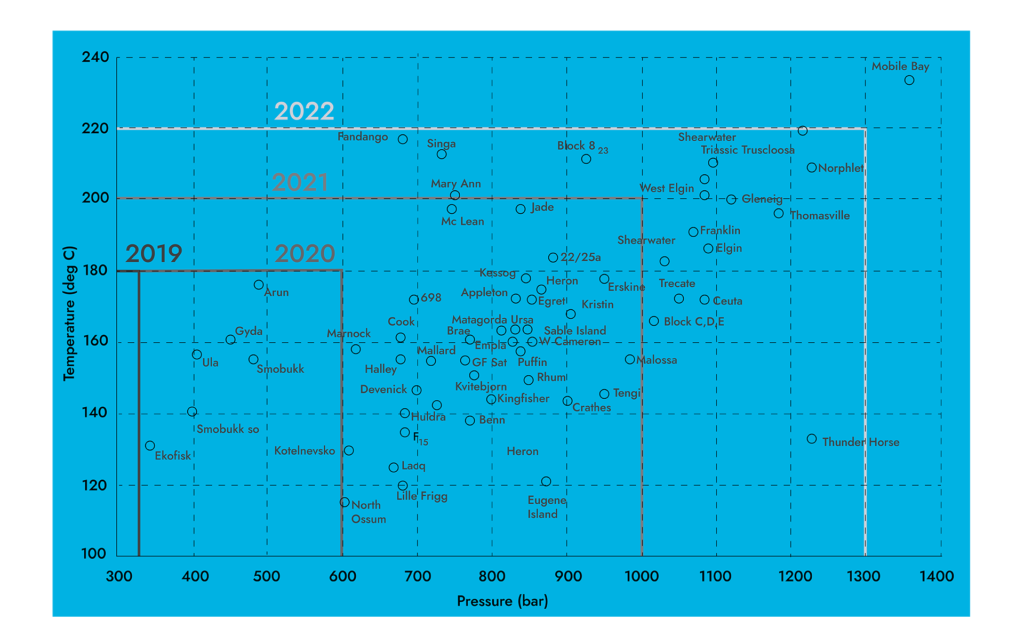
Interface’s portfolio currently includes:
- An MMP measurement that identifies the minimum pressure required for miscible oil displacement and enables gas optimization for minimum miscibility enrichment.
- Chemical EOR Optimization, which helps improve your chemical selection at reservoir-relevant conditions and confinement.
- A Flowback suite that provides fracturing fluid optimization to help select top-performing additives and minimize reservoir damage
- Regain Conductivity screening, which helps rapidly screen and optimize friction reducers to quantify damage, assess compatibility and optimize loadings
- Steam-assisted gravity drainage (SAGD) fluid performance screening helps select the solvent, alkaline additives, or non-condensable gases to supplement steam injection
- Asphaltene screening, which detects asphaltene onset under different reservoir conditions
- Rapid bubble point and dew point testing for retrograde condensate reservoirs or surface facilities
- A wax appearance temperature analysis that can result in better flow assurance by understanding wax onset conditions
Interface Fluidics is at the helm of progress
Microfluidic technology is being adopted by oil and gas laboratories around the world as a rapid method for screening oil and gas fluid properties and quantifying how fluids interact in rock. But it’s a challenge to operate these tests reliably at the high temperatures and pressures relevant to hydrocarbon reservoir conditions.
Interface Fluidics brings advantages like a quick turnaround, high operating pressure/temperature, and extensive knowledge of reservoir engineering in shale, offshore, conventional, and oil-sands reservoirs.
The rapid, robust, accurate, and accessible fluid measurements characteristic of microfluidics have much to offer the energy transition ahead. These platforms provide an exceptional opportunity to inform the operators and help the industry and decision-makers move forward – a role that is now more important than ever.