Introduction
From 2000 to 2014, the volume of water typically used for fracing an oil well in the United States increased from 177,000 gallons to over 4 million gallons. This surge in demand, combined with concerns over the depletion of freshwater aquifers is leading oil and gas producers to increasingly use produced water when designing chemical packages for hydraulic fracturing operations.
Although this shift is environmentally beneficial, produced water introduces many new uncertainties. Hydraulic fracturing fluids must be pumped at high flow rates to effectively transport proppants and create a fracture network. To achieve these rates while maintaining manageable pump pressures, friction reducer is added. However, produced water is well known to reduce the efficacy of typical friction reducers for several reasons:
Decreased Polymer Solubility:
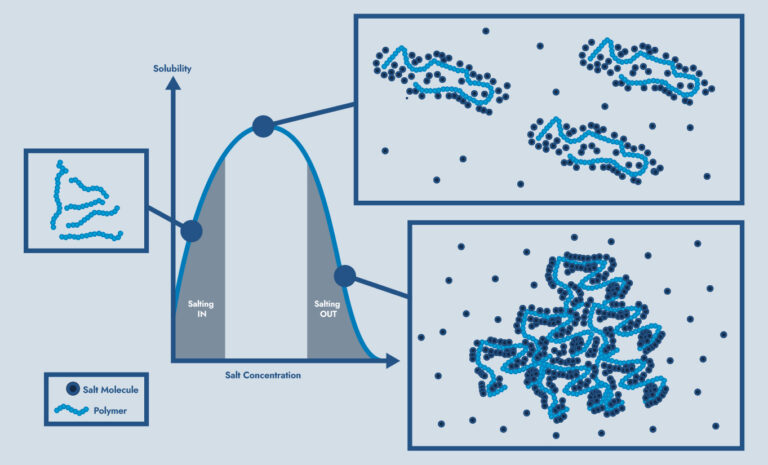
Bridging of Polymer:
Some ions can tangle up friction reducing polymers, preventing the “smooth” structure needed for effective friction reduction.
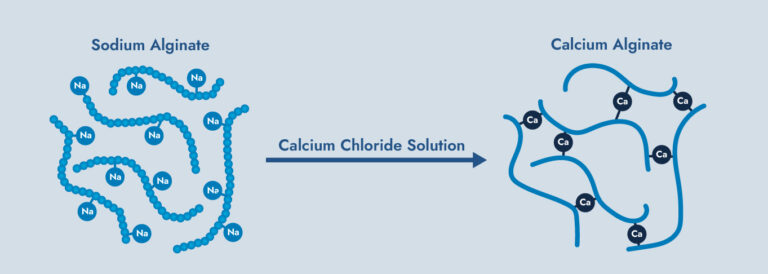
Complexity of Effects in Polymer:
Depending on brine composition and concentration, different effects are dominant leading to systems that are complex and not easily predicted. At lower salt concentration salting-in and electrostatic bridging are dominant while higher concentration is dominated by the salting-out effect.
Effects on Some Surfactants:
High-salinity brines can lower the surfactant concentration required for micelle formation.This occurs as the salt ions screen the electrostatic repulsion between the charged heads of the surfactant molecules allowing tighter packing of surfactant molecules.
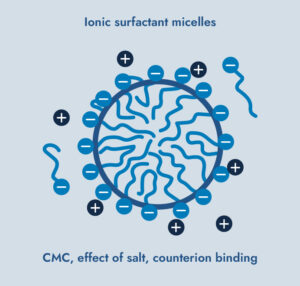
The Impact of Nano-Confinement
It is hard to wrap your head around just how small the pore throats are in a shale reservoir. Unlike conventional reservoirs with pore sizes in the tens of microns, in shale fluid travels through channels that are 1,000 times smaller. In these nanochannels fluid can behave differently. The phase behavior of fluids can change substantially with bubblepoint being suppressed in some published nanofluidic tests. At this confinement level, some fluid additives, like nanoparticles, or surfactant micelles can clog porous media if fluids are improperly selected. Surfactants can also adhere to the channel walls materially changing the permeability. With a larger channel, the impact of a layer of surfactant would not be material.
Designing Fluid Packages for Produced Water Use
The increased complexity of designing fracturing fluid blends in a world where produced water chemistry varies widely, leads completions engineers to move away from a one-size-fits-all approach. Instead, they are focusing on developing chemical blends tailored to the unique chemistry of each water source.
Historically, chemical manufacturers have relied on testing conducted with tap water to benchmark their chemistry, potentially leading to unrealistic performance in Total Dissolved Solids (TDS) water environments.
The complex interactions between each dissolved solid in produced water and every friction reducer, biocide, or surfactant remains poorly understood. Developing a chemical package based on best practices/experience is a good start, but the use of a comprehensive lab-based flowback screening program has been proven to consistently yield better results in numerous documented cases.
Interface fluidics has developed a novel chemistry optimization approach utilizing microfluidics and nanofluidics. Interface’s Flowback testing offers several key advantages over other tests:
- Actual fluids: Testing is conducted with the operator’s formation brine, produced water, frac chemistry, and oil.
- Representative Temperature and Pressure Conditions: All tests are done at reservoir temperatures with pressures high enough to ensure that fluids are in the same phase (liquid/gas) that they are in the reservoir.
- Representative Nano-Confinement: Nanofluidic reservoir analogues mimic target pore throat dimensions.
- Representative Wettability: Nanofluidic reservoir analogues are modified to approximate the reservoir’s wettability, allowing for measurable wettability changes.
- Capturing Temporal Effects: Chemicals are exposed to the reservoir analogue for extended periods, enabling observation of surface chemistry changes, impacting oil recovery rates.
Impact of Interface Fluidics’ Testing in the Field
Whitepaper: Optimization of High TDS Brine Frac Chemistry in the Wolfcamp with Primexx
In 2020, Interface Fluidics’ collaboration with Primexx in the Wolfcamp formation demonstrated the optimization of fracturing fluids. The focus was on reducing costs and enhancing chemical selection for varied conditions. The study highlighted the challenges of using produced water in fracturing, in particular the effects of high TDS brines on chemical performance, particularly surfactants and polymers. The paper details the application of Flowback testing to rapidly evaluate and optimize chemicals in high saline environments, resulting in significant cost savings and improved well performance.
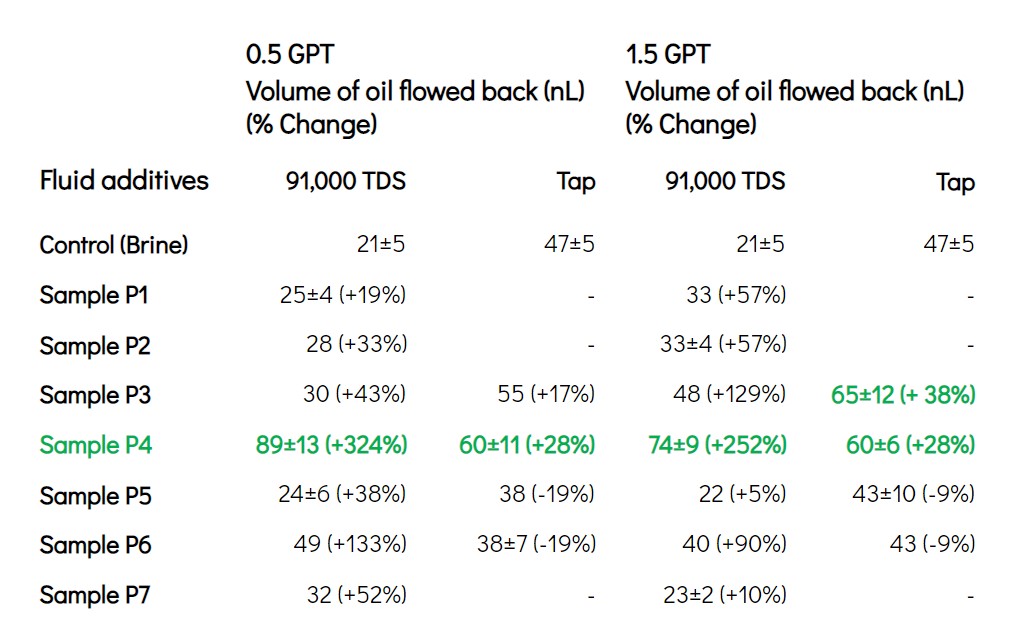
Conclusion
The interactions between produced water, friction reducer, surfactant, biocide and oil under various conditions of temperatures, rock wettability, and confinement are extremely complex and not fully understood. Optimizing fluids injected in hydraulic fracturing when using produced water should be done at a well-by-well level to minimize chemical spend, minimize reservoir damage, and maximize production.
Interface Fluidics has established our Flowback testing as an effective solution for chemical companies and oil producers ensuring optimal decision-making and a maximum return on investment.
Echoing one of my favorite movies, ‘Back to the Future’, let’s unlock the potential of underground energy resources like Marty McFly and Doc Brown unlocked the potential of time travel. Together let’s drive the energy industry forward, not just predicting the future of energy resources but actively shaping it