Steam-Assisted Gravity Drainage (SAGD) employs the horizontal well pair drilling technique to inject steam into bitumen formations. SAGD involves injecting a large volume of steam from the upper horizontal well, transferring a large amount of heat to bitumen via steam latent heat. Consequently, the viscosity of bitumen drastically declines, making it sufficiently mobile to drain by gravity to the producer (i.e., the lower horizontal well). Since the first SAGD wells were drilled in the 1990s, companies have wanted to make the process more efficient.
The key underlying mechanism behind the success of the SAGD process is in-situ oil viscosity reduction by increasing its temperature via steam injection. The main limitation of the SAGD process also stems from this same mechanism. To reduce the oil viscosity, the SAGD process requires high water and energy consumption. Introducing chemical additives to the injected steam is widely regarded to be a potential solution to mitigate this limitation by increasing the efficiency. Many different steam additives have been studied and used with varying levels of success. These additives can mainly be classified as solvents, surfactants, and non-condensable gases. We’re going to explore these technologies and dive into how they work.
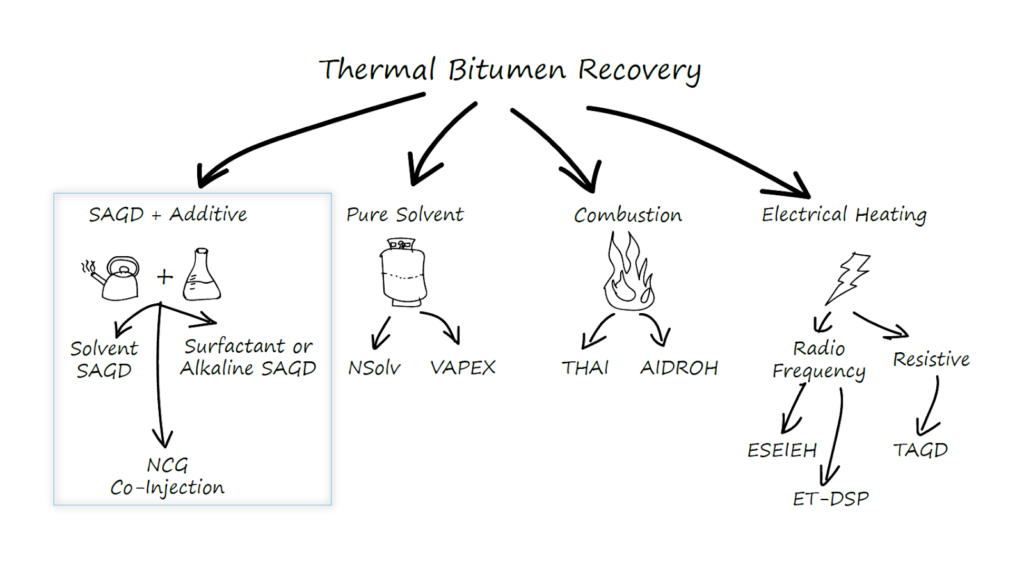
Solvents:
Solvents can be added to steam or heated and used without steam. Some typical solvents that are used by operators include propane, butane, diluent, or naphtha. Solvents improve the oil production rate by reducing the oil viscosity and sometimes by dropping asphaltene in the reservoir. There are many processes that implement this technology, namely, Expanding Solvent-SAGD (ES-SAGD), Solvent-Aided Process (SAP), Vapor Extraction (VAPEX) and N-Solv.
Viscosity: The solvents condense at the interface of the steam chamber, mixing with oil. This helps in reducing the viscosity of oil in addition to the reduction caused by increased temperature. In this way, the amount of water and energy consumption of the SAGD process can be significantly reduced.
Asphaltene: In technologies that involve solvent injection with little to no steam, depending on the solvent selection, asphaltene can precipitate out of oil. Asphaltene precipitation, which is often regarded as a problem in the industry, is also sometimes argued to improve efficiency of in-situ oil recovery processes. Drop out of asphaltene from oil in-situ has been shown to improve oil quality and reduce its viscosity. However, asphaltenes may result in pore throat blockage, hindering the steam chamber advancement.
Surfactants:
In the SAGD process, depending on water mobility into the reservoir the water condensation front at the steam interface can vary from a few centimeters to meters. Although water encroachment into bitumen can improve heat transfer through darcy-convection, it also can halt the oil production at the interface by reducing the oil mobility. Surfactants can improve oil mobility by changing the wettability.
Surfactants can be classified into ionic and non-ionic categories due to the presence of charged and neutral hydrophilic parts, respectively. However, the harsh pressure and temperature conditions pose steep challenges to the use of surfactants as additives in the SAGD process. Factors such as thermal stability, compatibility with reservoir fluids, oil recovery, and adsorption of surfactants should be carefully evaluated in the surfactant screening process.
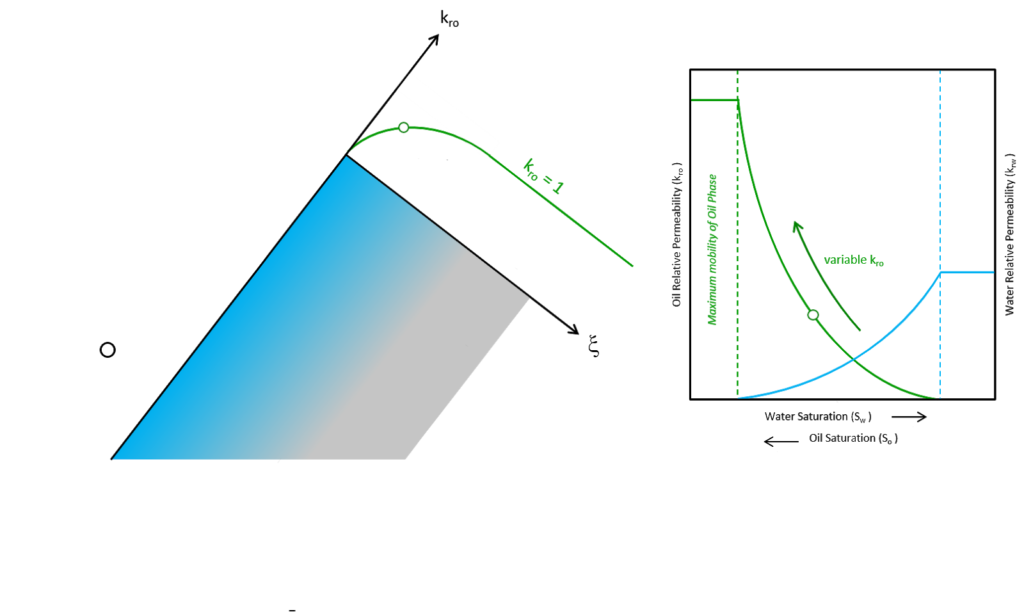
Non-Condensable Gas:
Co-injection of non-condensable gas (NCG) with steam is believed to provide several benefits in the SAGD process, such as higher energy efficiency, and the ability to maintain pressure in the reservoir. Gases such as nitrogen, carbon dioxide, and/or methane, are generally considered as good candidates as NCG additives. Studies of NCG co-injection have shown that the injected NCG tends to accumulate at the top of the steam chamber. This gas blanket is said to act as a good heat insulator that prevents heat losses from the steam to surroundings at the top, thus increasing the energy efficiency of the process. In addition, due to partial pressure effect operators can raise the chamber pressure at less energy supply, that creates better pressure support and higher drawdown pressure on the producer.
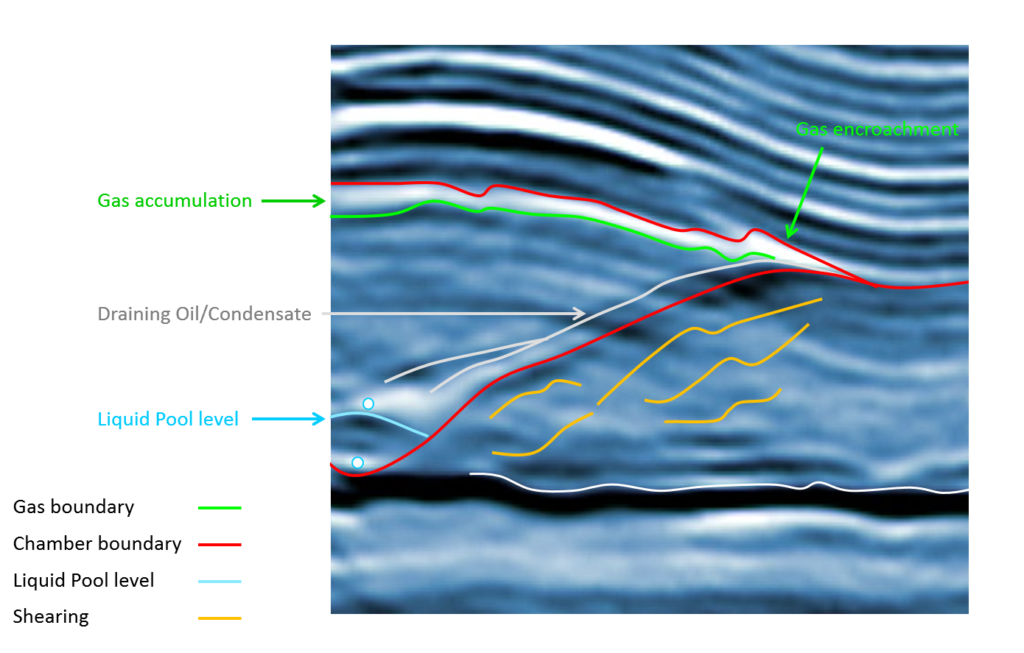
Today, the need for more efficient in-situ methods for bitumen extraction has been stronger than ever before due to the current low oil price environment and the ever increasing demand to reduce greenhouse gas emissions. Testing these methods in process simulators and labs are a great first step towards finding a method that is not only efficient but also tailored for the specific reservoir under investigation. Simulation and lab results enable data-driven selection of candidate methods for field pilot testing, which can significantly enhance the chances of success in the field.
About Ashaw Energy
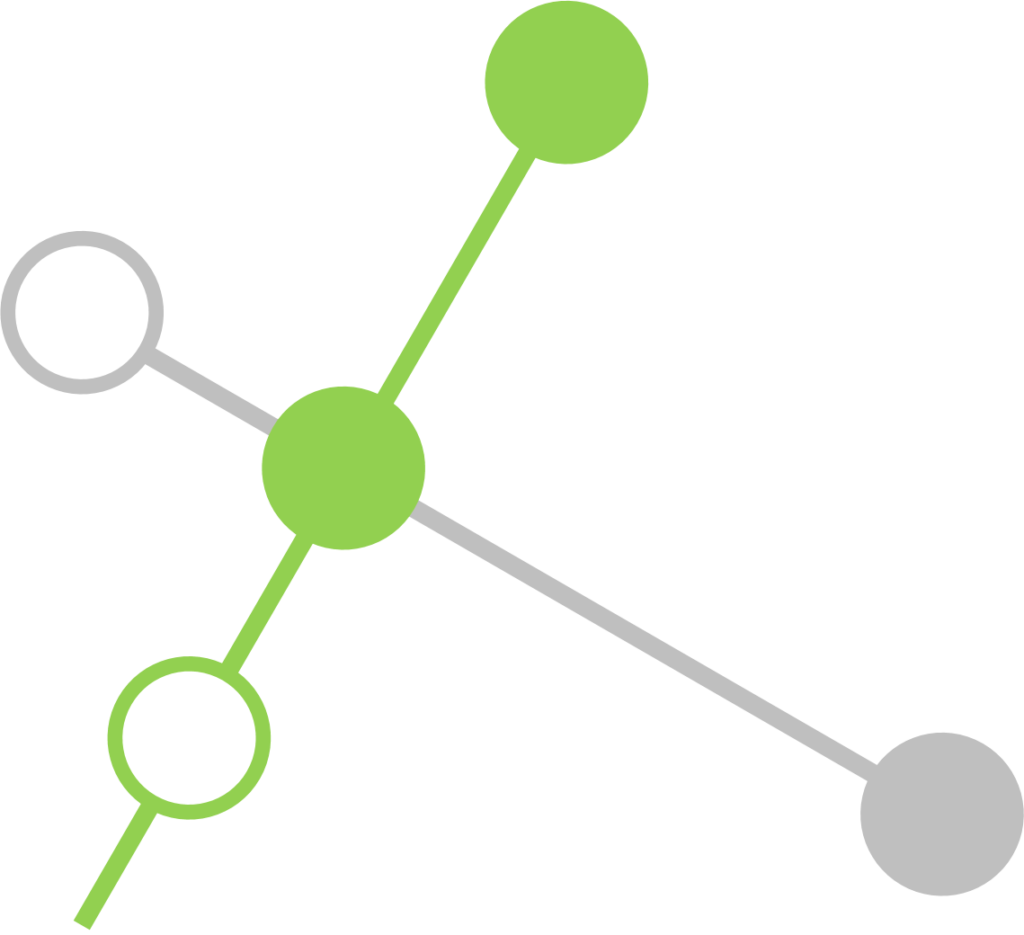
Ashaw Energy is an upstream petroleum engineering Software Company was founded in 2017 and has expanded across the major plays in North America and into international. At Ashaw Energy, our purpose is to model and conduct automated history-match for a multi-well reservoir from downhole to surface in a fraction of a minute.
About Interface Fluidics
Interface works with energy companies and chemical companies to evaluate reservoir enhancing chemicals and processes. Interface’s service has helped oil and gas operators in North America, offshore Norway, and the Middle East, decide how they optimize their wells to increase productivity.
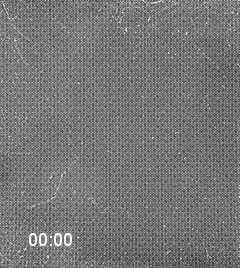
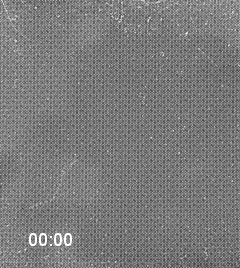
By: Sourabh Ahtian*, Mazda Irani**, Tom de Haas*, and Ali Abedini*
*Interface Fluidics
**Ashaw Energy