Hydraulic fracturing – or fracking – is a technique used to access tight reservoirs by blasting water, sand, and chemicals into the formation, breaking them open, and allowing oil and gas to flow back to surface. The hydraulic fracturing fluids used are a sort of cocktail of chemicals from friction reducers and biocides to surfactants and nanofluids.
The chemicals added to a fracturing fluid each serve different purposes, whether that’s wettability modification, interfacial tension reduction, corrosion prevention, or improved recovery. Additionally, every well or well pad has a unique blend of chemistry, designed to meet desired performance targets.
But what happens if the chemicals added to improve production performance result in formation damage? A professor of mine once referred to this as a “CEM” or “Career Ending Move.” (Funny enough until it happens to you.) Career goals aside, formation damage, while unavoidable to some extent, is something many of us in the industry are working to minimize.
Formation damage impairs the permeability of a formation and consequently reduces the productivity of the reservoir. Depending on the mechanisms of formation damage at play, the impact varies from well to well.
Regardless of the severity, any reduction in productivity is undesirable. Formation damage is caused by a number of different mechanisms. There are four main categories of formation damage including chemical, thermal, mechanical, and biological.
Using Interface’s Flowback solution, we can screen through fracturing fluid additives and fluid combinations – at reservoir temperatures and pressures – to identify which additives improve performance, and those that may damage your reservoir.
Our visualization techniques are particularly helpful in identifying chemical incompatibilities and thermal damage that may go otherwise unnoticed in traditional test methods like core flooding and column drainage tests.
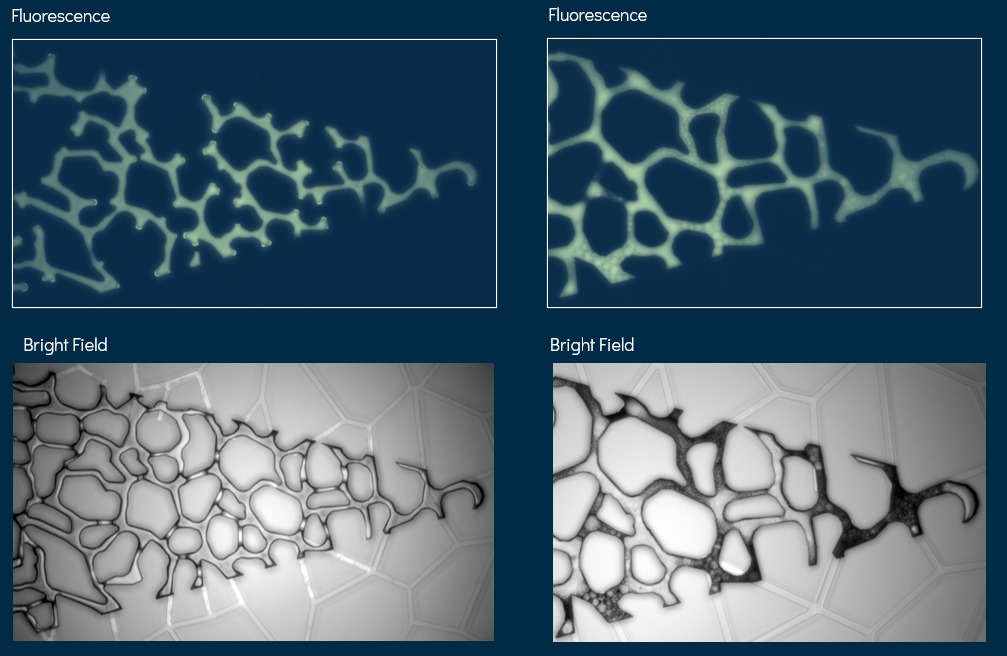
Chemical Incompatibility
Chemical damage mechanisms generally occur due to undesired rock-fluid interactions, fluid-fluid interactions, and near well-bore wettability alteration. Fluid incompatibilities between injected and formation fluids can cause emulsions, precipitation, and sludge that block up the reservoir pores.
Drilling and completions fluids also contain solids that may be incompatible with the reservoir fluids. This is why our Flowback test uses your reservoir-specific oil and water samples – helping you quickly screen through frac fluids that will be compatible with your reservoir.
Wettability alteration, while often sought after to lower wettability in oil-wet reservoirs, is another way in which formation damage may occur. Chemistries that are added to your fracturing fluid – like corrosion inhibitors, surfactants, and solvents – can invade near wellbore regions and result in a more oil-wet system. This means that your reservoir now prefers to produce water, rather than the oil that you are drilling for.
Interface’s suite of testing enables us to identify the wettability alteration that occurs during fracturing by measuring contact angles within the porous media before, during, and after injection. This helps you select a chemical with your desired wettability effects, rather than one that will minimize production.
Variables affecting chemical damage include the chemical package, injected water, in-situ water and oil, reservoir temperature and pressure, wettability alteration, rock properties, and clay incompatibility.
The ideal platform for this screening needs to fulfill a few criteria.
• It needs to yield reproducible results that are independent of the operator.
• It should provide the ability to control as many variables as possible to isolate each parameter’s impact.
• It should have established uncertainty values and provide high-resolution results.
This level of control was rarely seen or even possible in oilfield labs until Interface came along to fill in the technological gap.
When thinking about optimization, a multi-staged approach is recommended. At a very basic level, the frac cocktail can be screened for compatibility with the injection brine. With advancement, the interactions between the frac fluid, in situ oil, and porous media itself can be studied. Finally, inter-well fluids can be tested for compatibility.
Thermal degradation
Thermal degradation occurs at high temperatures (where chemicals can destabilize or break down) causing precipitation/deposition and ultimately formation damage. Bench-top laboratory testing often can’t account for the thermal impact on chemical performance, but Interface Fluidics screening – done at reservoir temperatures – does.
One of our U.S.-based clients was seeking specific surfactant products applicable to the Eagle Ford reservoir conditions and were given several choices by service companies and chemical vendors.
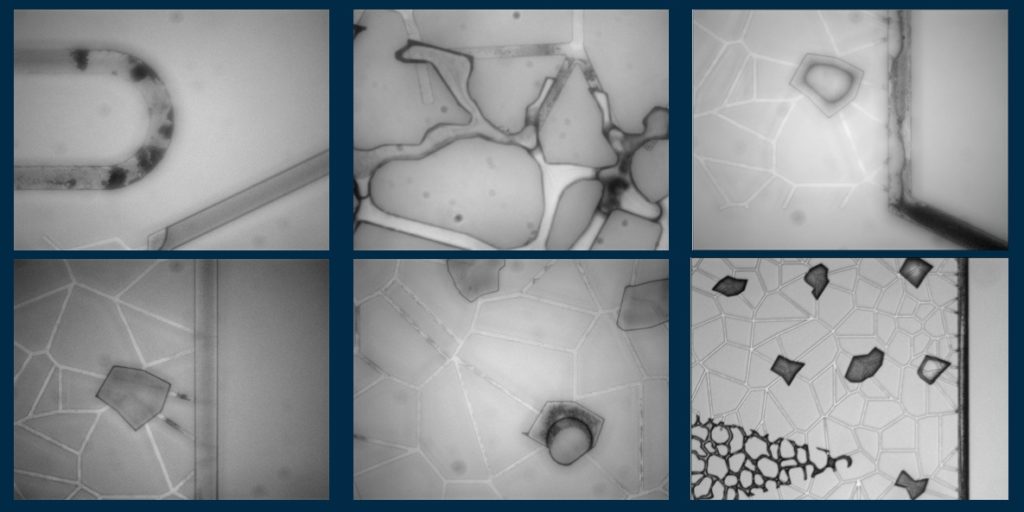
Conventional laboratory testing couldn’t provide stability data or the surfactant performance at reservoir temperature. Because of this, a decision was made to utilize microfluidics technology comprised of reservoir rock properties, including pore size, permeability and porosity values, wettability parameters, water composition and oil from the well test area.
This would provide a necessary first pass to see whether or not any of the surfactants had the potential to improve recovery at reservoir temperature and pressure – and if the cost of implementation would be acceptable.
Because of the Eagle Ford’s challenging conditions, a highlight Interface’s screening is the ability to mimic the conditions. This particular reservoir had a low permeability with small pore-throats, high reservoir temperature of ~300 ⁰F, and the wettability was intermediate- to oil-wet.
Four of the six products tested, at two different concentrations, resulted in significant damage by forming solids and plugging the pore-throats. Some products completely blocked the analogue, not allowing any oil to flowback.
Seeking to fill the unfortunate gap in the market, Interface uses its Flowback solution to rapidly screen fracking fluids at high temperatures and pressures – allowing clients to feel more confident in the chemical selections.
By identifying the top performing chemistries (and which ones to avoid) based on oil production, wettability alteration, and damage formation, Interface provides faster, more repeatable, and more cost-effective solutions.
Note: If the video does not play, please visit https://www.youtube.com/watch?v=sXqLEZi5Nfo
Friction reducer conductivity testing
In another project, we worked with Rockwater to screen six friction reducers (FR) and isolate the impact of breaker, temperature, liquid vs. powder FR, brine salinity, and stabilization time on conductivity testing.
This 12-day commitment involved 20 conductivity tests, reduced turnaround time by two months, and lowered cost by more than 50% compared to conventional methods.
Results of this work showed most FR preferring breakers, and broken reducers, producing less damage and taking less time to stabilize. Insights helped address solubility of FR, the occurrence of infectivity problems, and long-term performance.
The method we developed offered much higher repeatability compared to proppant pack tests, an incomparably faster turnaround, at a much more affordable price point – while using a fraction of the sample size.
Gummy bears – not as fun as they sound
At Interface, we’re looking at both the prevention and remediation of gummy bears, or the mystery gunk that may be coming out of your well. Of course, prevention is the preferred choice.
When we talk about prevention, we’re looking at ensuring the brine chemistry and additives are compatible, looking at iron sensitivity, and optimizing friction reducer selection and breaker loadings to prevent gummy bear formation.
- Brine chemistry
- Iron sensitivity
- Friction reducer selection (low MW)
- Breaker loadings
- Additive compatibility
- Chemical treatments
- Swanson, et al. (2018) reports very positive results from pumping chemical remediation treatments in damaged parent wells in the Woodford
A study by the National Energy Technology Laboratory found evidence that iron can also react with surfactants, undercutting the ability of those additives to increase oil production.
Still, experts who have studied problems blamed on friction reducers complain that these additives are regularly evaluated by the industry based on tests in tap water, where they generally perform as promised.
Creating a realistic test for widely used fracturing additives will require meeting a huge challenge: Describing the chemistry of a typical shale play. At Interface, we can create a gummy bear in our device, and look at different chemical cocktails to clean up the problem.
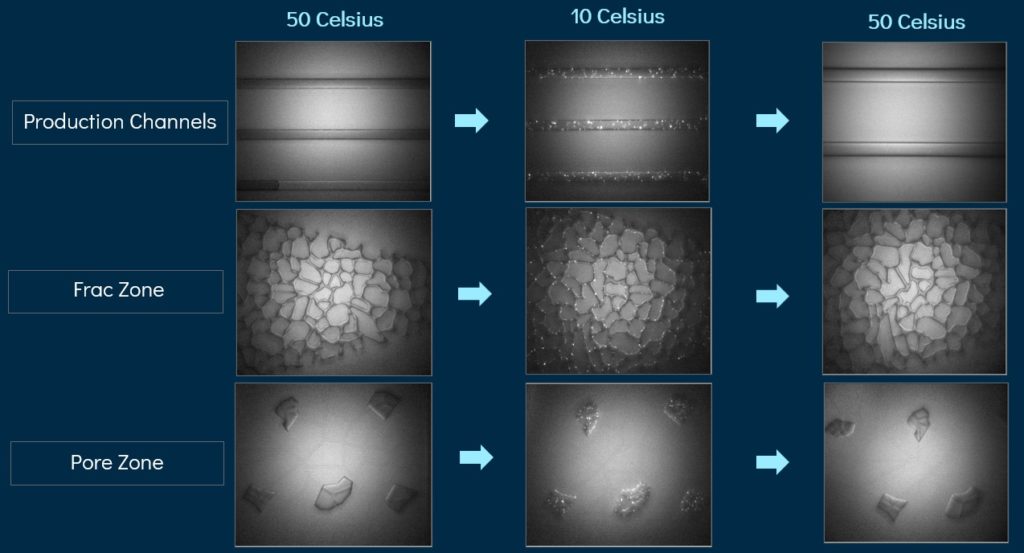
Wax appearance temperature
Another aspect of flow assurance industry professionals require is an investigation into wax onset conditions.
To analyze the impact of wax damage, this experiment took a 3-stage approach. 1st stage is initial volume of oil flowback at 50 ˚C (no wax damage). This is followed by testing at 10 ˚C (wax deposition). Then the system is made to go back to its initial temperature of 50 ˚C to observe if any irreversible damage occurred.
What we found was a 23% reduction in oil volume even when conditions were returned to pre-precipitation levels. This suggests that wax appearance is not a fully reversible process as commonly believed.
At Interface Fluidics, our goal is simple. We want to help the oil and gas industry make better cost-saving completions decisions that help improve hydrocarbon recovery, reduce fracturing fluid costs, and ultimately increase the return on investment.
By using our microfluidic technology platform, we screen flowback fluids and identify top-performing additives, which helps you to optimize your fracturing fluids spend and avoid fluid dosing and combinations that can damage your reservoir.