The oil and gas sector’s digitization presents an opportunity to the tune of $2.5 trillion of value – and over a billion tonnes of emissions and 800 million gallons of water-use reduction by 2025. However, the World Economic Forum reports the industry has been slow to adapt to the ongoing digitally-fueled transition.
Software innovations driving this transformation include the Internet of Things (IoT), big data and analytics, system integration, computer vision (CV), and automation. By incorporating these advances, old-school industry can streamline operations from the wellhead to the gas pump.
Similarly, fluid testing companies servicing oil and gas are stuck conducting analysis with decades-old technology. As a next-generation reservoir fluid testing company, Interface Fluidics uses innovation to realize a competitive advantage – breathing new life into the petroleum industry.
Pushing the envelope on fluid screening
The first step in a hydrocarbon operator’s decision-making process should be fluid testing. This is crucial in the exploration and production stages, impacting surface facility designs and full-field development.
While conventional tests have seen some incremental advances, they still rely on concepts dating back to the 1930s. This includes spending millions to extract a core and many more to extract the liters of samples needed to conduct a handful of measurements.
At Interface, we use nanotechnology to replicate the reservoir rock instead of extracting it. In doing so, we create analogues to test fluids at reservoir-relevant conditions. Combining these microfluidic chips with high-resolution optics helps reduce sample volume and measurement time, alongside many other advantages.
Interface starts fluid-fluid compatibility studies by gathering reservoir-rock properties, including permeability, porosity, wettability, and pore size, which we capture on a CAD design. The next step is to turn this design into a physical chip using nanofabrication.
Here we use photolithography, followed by deep-reactive ion etching, to create reservoir analogues made from silicon. Then we bond glass to the silicon substrate using anodic bonding. Finally, we put all finished chips through a quality control matrix.
Once the device is ready, we inject several pore volumes of reservoir fluids and conduct experiments under powerful digital microscopes. We then process the image results through computer vision to quantify chemical performance. By doing so we can measure a chemical’s potential for increasing yield or creating damage.
But our capabilities don’t stop there. After six years of continuous innovation, Interface can now hit 15,000 psi and 390 °F – allowing us to operate in over 80% of the world’s reservoirs.
We’ve also rolled out the portable laboratory bench SapphireLab, enabling our tests to be run on-site. While SapphireLab is more advanced, compact, and convenient, the chip fabrication, running of experiments, and the software behind it and our in-house testing services are the same.
Interface’s software comes in three parts: Autobench, Autoanlaysis, and Portal. Together, these provide a comprehensive set of tools needed to run tests, manage operations, and analyze large sets of images from microfluidic tests.
Speaking of software, Industry 4.0 is an umbrella term that has come to encompass the most exciting trends in digitization. These include IoT, analytics, CV, and automation.
But how is it relevant to the energy industry?
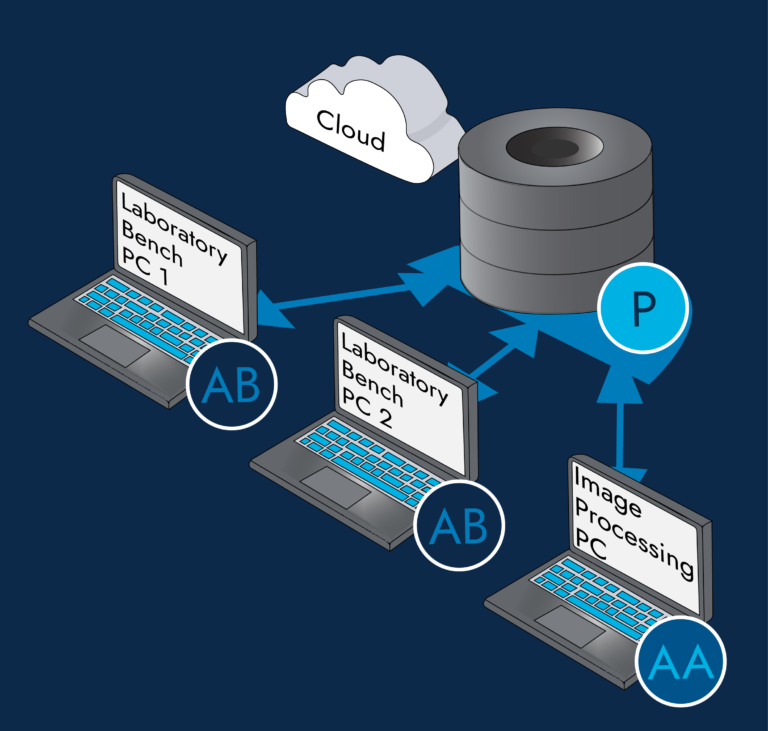
IoT oil and gas
IoT is a network of physical objects connected to the Internet. These objects are embedded with sensors, software, and connectivity to the cloud, enabling data transfer without human interaction – leading to otherwise-impossible volumes of data collected.
The average oil platform uses 80,000 sensors which generate more than 2 TB of data per day. IoT is useful in drilling management, pipeline, refinery, offshore monitoring, health and safety, and carbon footprint control.
It is a valuable tool in the arsenal of forward-thinking companies, which is estimated to boost reservoir production by 6-8% when combined with data analytics. A survey by Microsoft found that 86-90% of oil companies believe that analytical, mobile, and IoT technologies add value to their business.
For similar reasons, IoT is a core element of Interface’s Autobench software. Using it, lab technicians can safely integrate hardware from different manufacturers, adding an additional layer of flexibility with the unified logging, control, and automation of microfluidic hardware.
Autobench for oil and gas big data and analytics
The biggest Autobench feature is the consolidation of big data. This includes instrumentation, camera-visualization, and user-auditing information. Instruments covered include pressure sensors, pumps, temperature controllers, valves, and other components.
There is a lack of universal software that perform these functions. Current options available on the market are complex, cumbersome, archaic, and require specialized training, producing accessibility barriers. Because of this market gap, we put a team together and invented our own platform.
For analytics, we integrate the data and then analyze it to compare test performance against a range of variables to get actionable information, troubleshoot problems, and improve designs in future iterations.
Another part is gathering user audit logs. So anytime a user makes a change, it’s recorded. Software can then be applied to this data to create graphical representations that can improve the software, find bugs, and identify cases of human error.
Computer vision oil and gas
Developed to emulate human visual cognition, CV is vital for task automation. It has evolved to the point where it can interpret and understand complex images with 99% accuracy.
Because of its amazing potential, the global market for this technology is expected to reach $41 billion by 2030. The main driver behind this growth is the capacity of CV to process massive amounts of visual data very quickly.
At Interface, our Autoanalysis software is an image processing system focused on extracting data from microfluidic images. It can import data from the database shared with Autobench and Portal.
With this tool, one can design, save and perform routine analysis on image stacks from multiple tests in batches. Autoanlaysis can grab data from every piece of equipment and correlate it with images from each test. Using computer vision streamlines tasks that would normally have to be done semi-manually, improving operational timelines.
Using this technology, lab techs no longer need to sift through thousands of images and conduct analysis and consolidation. Instead, they simply record the information and easily navigate the data the software produces.
Automation oil and gas
Automation is a software practice that deploys algorithms that emulate human actions while interacting with digital and physical systems. It makes processes and operations more resilient and agile, so businesses can adapt to change while cutting down on labor and human errors.
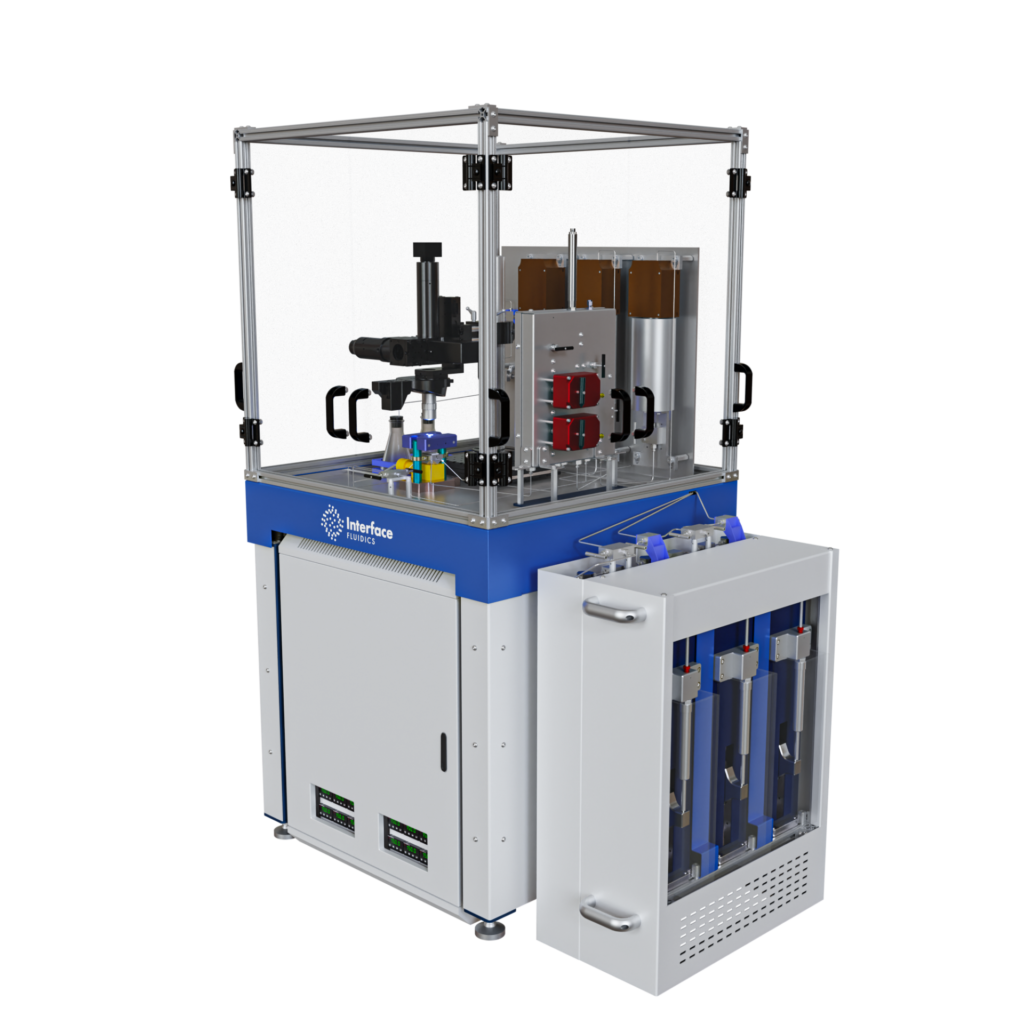
A 2022 study found that most global executives believe automating workflows ensures business continuity and gives companies a competitive advantage. For the petroleum industry, the automation market is expected to surpass $24 billion in just a few years.
Using Interface’s Portal, automating tests becomes a very user-friendly feature.
Portal is a centralized hub for managing a microfluidics lab. It provides a web-based environment to plan and monitor activities, schedule and monitor chip fabrication, and manage inventories. It may also be used to set up automated tests through the recipe system.
Creating recipes incorporates all three software applications. Portal allows users to create reusable recipes with editable steps.
When used with Autobench, recipes can be built and executed – allowing for consistent operating conditions and full test customization. Autoanalysis improves recipe saving and can scan the database for changes and execute recipes when needed.
The potential to transform
Technologies like IoT, CV, and automation are having a monumental impact on hydrocarbon extraction – and we’ve only scratched the surface of their potential to transform the industry. With the digitization market undergoing a boom, technology that might have been far-fetched ten years ago is now the competitive edge companies seek.
Whether we’re commercializing nanotechnology-enabled testing for energy or helping with CCS and hydrogen, Interface stands at the forefront of innovation. And as we continue to scale, next-generation software will play a pivotal role in streamlining operations and integrating systems.